4.0 Intelligent and connected machines: Soluciones integradoras para el rectificado digital
After 3 articles in which we have brought together the benefits and added value that its assets and services can offer Basque SMEs in the field of digital finishing, we put an end to the month of Intelligent and Connected Machines node with this article, which includes the opinion of its coordinator.
Rafa has a degree in Industrial Engineering from the University of Navarra, and has spent his entire working career at IDEKO, one of the most important technology centres in the Basque Country’s ecosystem, specialized in advanced manufacturing and with a strong European presence. He held the position of Director of Mechanical Engineering for almost 13 years, later becoming Director of Research and Technological Development, a position he has held since 2009 and which he combines with that of coordinator of the Intelligent and Connected Machines node of the BDIH. During his almost 25 years of experience in the sector, Rafa has been able to learn first-hand what the main needs of industrial companies are and how they evolve, and how the implementation of new technologies can contribute to improving their processes.
In this article, Rafa will show us the solutions that this node can provide to Basque industrial SMEs to improve their grinding processes, and will help us to better understand why this is such a relevant process and one to which companies should pay special attention.
As emphasized in the article introducing the node, the digital grinding process is particularly critical for manufacturing companies. Rafa assures us that this “is due to the fact that it is a process that meets particularly demanding requirements and characteristics”, since, in the first place, “it is a finishing process with very narrow geometric and surface quality tolerances, due to the high demand and responsibility under which the ground components will ultimately work in their functional life: precise movements, high speeds, wear, friction…”, on the other hand, Rafa tells us that “it is usually the last manufacturing process, which together with the narrow tolerances makes any error in grinding difficult to recover, the error leads to rejected parts, with consequences in costs, efficiency and waste generation”. This, makes it “technologically one of the most complex material removal processes, due to the removal mechanism, the contact geometry and the kinematics and dynamics of the diamond-wheel-worker-machine interaction, making obtaining the correct process and optimizing it particularly complex”.
In this sense, the equipment, services and assets offered by the node contribute to the improvement of factors that play a crucial role in the development of industrial activity, such as integrity, reliability, quality and productivity. The digital grinding process also takes on special importance in sectors producing parts with responsibility and added value, as mentioned above. Automotive, aeronautics, optics, precision mechanics and electronics, are sectors that integrate elements with precision among their components,
One of the main problems in the field of grinding are the surface defects generated during the process and which lead to the rejection of the parts, the most common being the “lead error” or propeller error, and the “waviness” or surface undulation. At this point the node coordinator is emphatic: “This surface defectology, not being the only one that occurs in grinding, is perhaps the most complex to resolve, because it is the most complex to characterize and identify the sources, which may be several and usually a combination of them. The identification of the sources and the resolution of the problem without losing the productivity ratio are challenges faced by both machine manufacturers and, especially, users in their production processes”.
The assets that the node makes available to Basque SMEs allow them to detect and solve these errors during the manufacturing process of the parts, avoiding having to use the trial-and-error method, with all that this entails in terms of efficiency, improved productivity, cost savings and reduced returns. Furthermore, the techniques adopted are non-destructive inspection techniques (NDT), which allow parts to be inspected without the need to destroy them, thus maintaining their physical, mechanical, dimensional or chemical properties. This is of great value, according to the declarations of the coordinator of the node, for “companies whose products include parts that are subject to safety requirements during their operation, with responsibility for failures that could produce serious production problems, as in the case of steelworks, cement factories, paper mills, energy production and transport in general, and even more so those on which the safety of people depends, such as aeronautics, railways, automobiles and transport in general, integrate into their production chains the verification of the integrity of the parts produced”. This verification is carried out both by destructive methods in the case of prototypes or demo parts, and by traditional means that are not very automated, not very repetitive and very dependent on the human factor. The new inspection techniques, based on ultrasound technology, eddy currents and others, allow progress to be made towards overcoming these limitations and even moving towards in-process integration of the inspection.
Another area in which the Intelligent Machines node can provide added value, is that of process and lubrication solutions. The appropriate use of coolants and lubricants is a key factor in the grinding process, influencing various aspects of the process: most obviously, avoiding thermal damage to parts during the grinding process, thus preventing phase changes and residual damage. No less important is the influence of correct lubrication on the efficiency of the cutting process, resulting in surface quality on the workpiece and tool life. Finally, grinding machine manufacturers use cutting fluid as a thermal stabilization element for their machines, to minimize geometric distortions due to the influence of heat sources or variations in ambient temperature. The importance of the formulation, selection and treatment of the cutting fluid is complicated by environmental aspects. Rafa concludes that “the grinding sector is by no means unaware of the development of strategies to reduce the impact generated by the use of cutting fluid: from the formulation of the fluid, through the reduction of its use, to the design of systems that increase the efficiency of its application, reducing both the volume of fluid and the consumption of pumping and filtering equipment, and ending with post-processing techniques”.
The digital grinding node has assets that enable it to address in the design, formulation, characterisation, application and post-processing phases, the management of cutting fluids, taking into account the aspects indicated.
The Intelligent and Connected Machines node currently has 11 assets distributed among the 6 organisations that make it up, and its coordinator, on behalf of the node and its components, is sending a message to the Basque industry: “We would like to invite companies active in the world of grinding: manufacturers of machines, grinding wheels and diamonds, components, cutting fluids, filtering equipment, and especially machine users, companies that use grinding to manufacture their product, to avail themselves of the services offered by the node, in terms of high-level customised training, development of new solutions, testing and pre-industrial validation or any concerns related to the grinding process and associated technologies. The node offers them differentiating assets and the knowledge in grinding of the researchers and technicians of the agents involved.
Contact the BDIH to find out how we can bring your company closer to the solutions that interest you most.
Related news
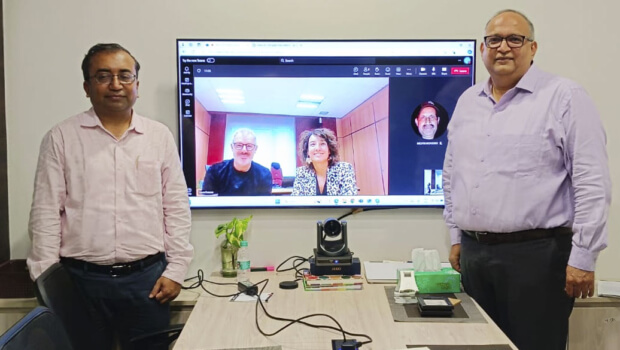
SMARTPM and SubAero Precision Machining announce strategic partnership in India
The collaboration between SMARTPM and SubAero Precision Machining (Group Designcell) is a big step in our global growth, helping us establish a strong foundation in one of the world's fastest-growing industrial markets
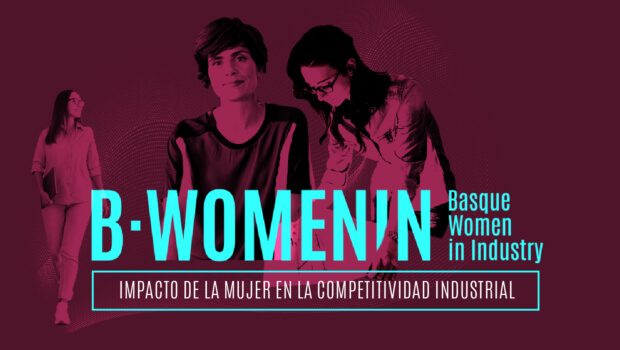
Companies with greater gender equality perform better in terms of innovation and are more competitive
The study of the SPRI initiative "Women in Industry" shows that gender equality has an impact on the improvement of company results.
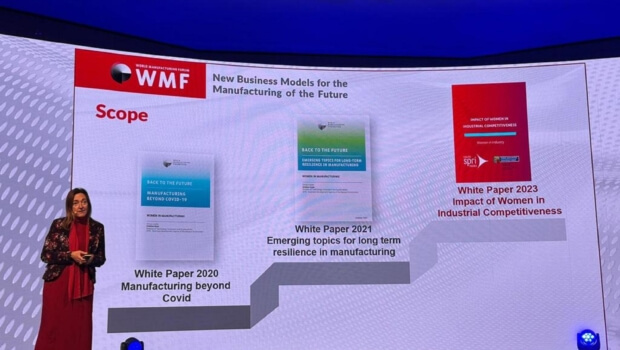
SPRI presents the results of the study on the impact of women on industrial competitiveness at the World Manufacturing Forum
The reports is the continuation of the work carried out by the SPRI Group and the Foreign Network office in Milan since 2020 as leader of the Women in Manufacturing expert group.
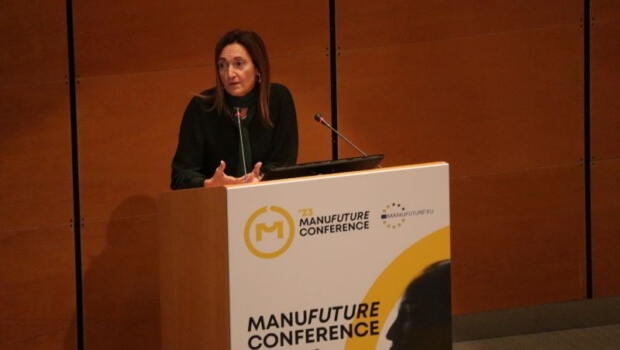
Europako fabrikazio-ikerketaren etorkizuna
Donostian, egunotan, MANUFUTURE Conference 2023 egiten ari da, hau da, fabrikazio-industriaren etorkizunari buruzko Europako konferentzia.
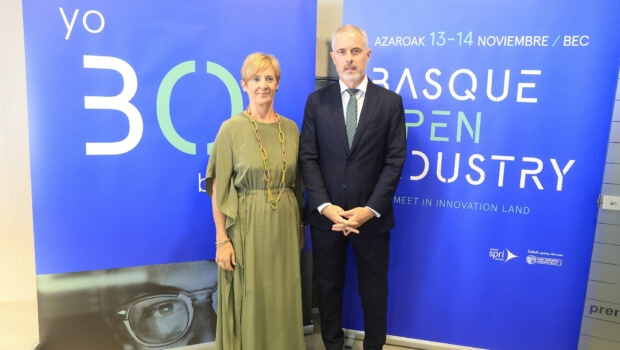
Basque Open Industry will show Europe its industrial and technological ecosystem at the European SME Week (SME Week) from 13 to 17 November.
Talent, internationalisation, energy-environmental and technology-digital transitions. SME Week 2023. Exhibition and stands at the BEC: “Rebuild Ukraine”.
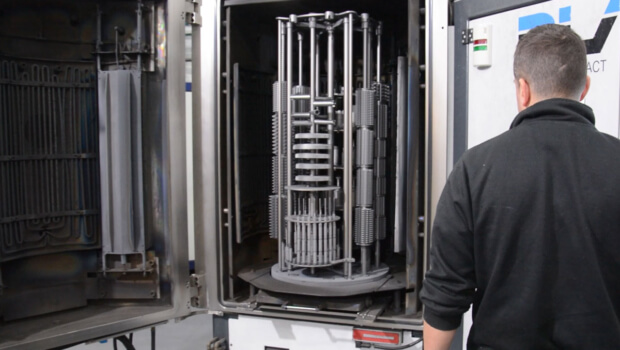
Get to know the assets of the BDIH: 5-axis multi-process milling cell, capable of very high speed operations
The University of the Basque Country offers Basque companies, via the BDIH, the possibility to have at their disposal a 5-axis multi-process milling cell, capable of very high-speed operations.
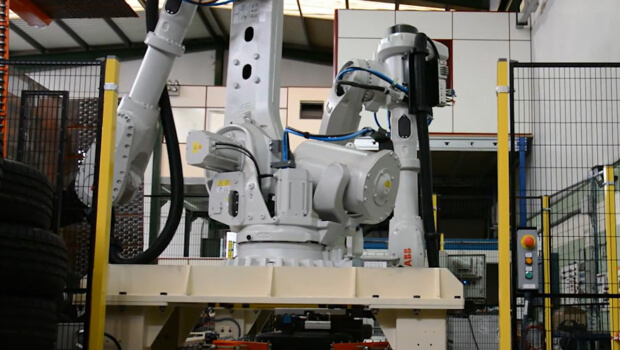
Get to know the assets of the BDIH: Inspection/measurement robotic cell using non-destructive techniques
Tekniker gives the opportunity to Basque companies, by means of the BDIH, of having at their disposal a cell which permits to carry out analysis for the quality control and the non-destructive inspection of pieces.
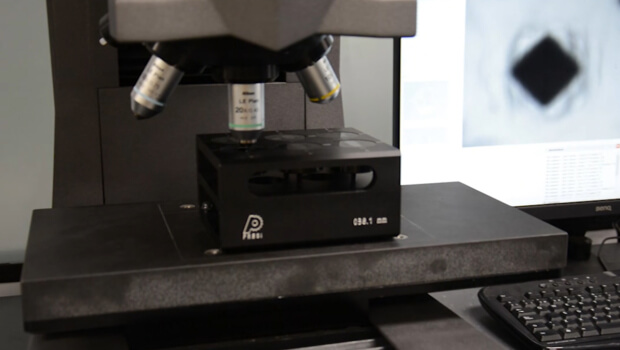
Get to know the assets of the BDIH: Equipment/Techniques/Methodologies for the study and evaluation of corrosion
Cidetec offers Basque companies, through the BDIH, the possibility of testing their materials with in the order to know their corrosive capacity. For this purpose, the asset uses accelerated and cupro-acetic corrosión climatic chambers, as well as electrochemical and localized techniques for the corrosion studies.

Get to know the assets of the BDIH: Systems for mechanical properties and microstructure determination by magnetic non-destructive measurements
CEIT offers companies, through the BDIH, the possibility of access to quality control systems to detect failures or inspect subsurface processes in a non-destructive manner, allowing costs to be reduced and avoiding wasting parts that could be sold
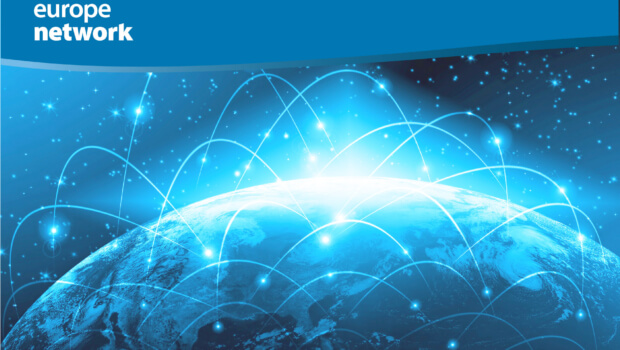
The Enterprise Europe Network offers Basque companies advice on technological development and the international commercialization of innovative products and services
The Enterprise Europe Network (EEN) has established itself as the perfect public sector tool to complement the efforts of Basque companies in internationalizing their R&D&i and their business in general. Through its advisory and assistance service in the transfer of knowledge, technology and innovation, more and more SMEs are seeing...